
Topografia
27 Gennaio 2019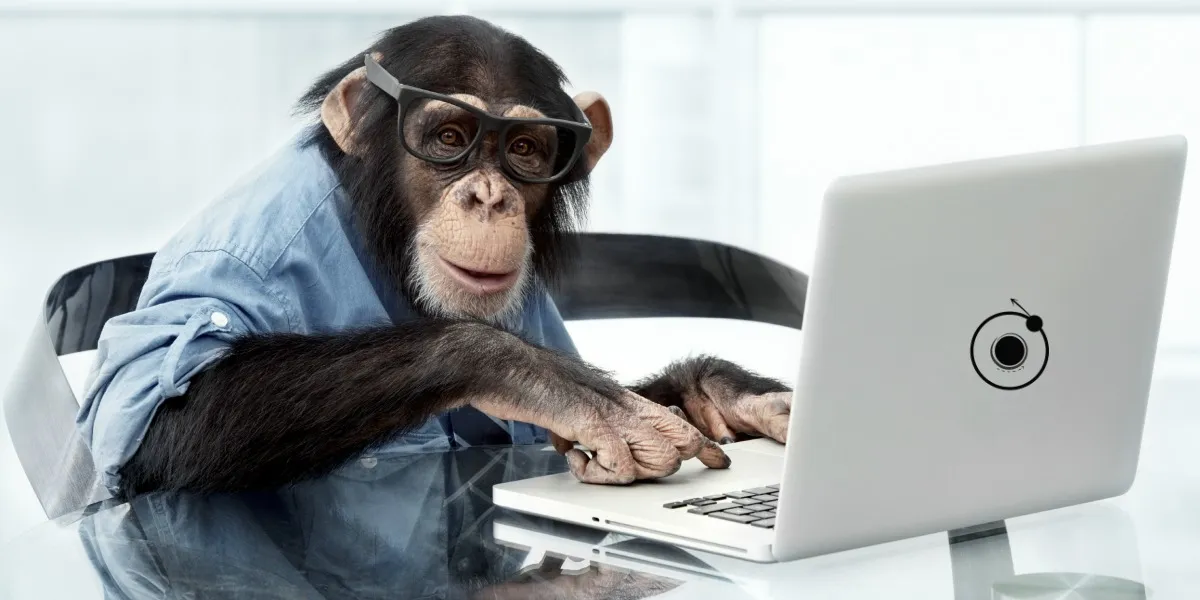
Charles Darwin e la Rivoluzione dell’Evoluzionismo
27 Gennaio 2019Abbiamo incontrato più casi rilevanti in cui il composto sintetico sostituiva quello naturale (alizarina, indaco); abbiamo anche visto che gli sviluppi dell’industria dell’azoto avevano sostituito l’acido nitrico sintetico a quello proveniente dal Cile sotto forma di nitro. In tutti questi casi le molecole sintetiche erano indistinguibili da quelle di origine naturale, ma avremmo potuto citarne altri in cui un particolare “effetto”, ad esempio fisiologico, era ottenuto con molecole di struttura completamente diversa da quelle della sostanza da “sostituire”. Così la saccarina o solfammide benzoica, sintetizzata nel 1879 da Ira Remsen (1846-1927), aveva un potere dolcificante circa cinquecento volte maggiore del saccarosio e, chimicamente, non aveva nulla a che fare con gli zuccheri. I processi di cui ci occuperemo in questo paragrafo sono vicini a questo secondo tipo di sostituzione, in quanto portano a sostanze che sembrano e non sono quelle “mimate”, e tuttavia questi processi anche se ne differenziano perché i materiali ottenuti sono appunto tali: di essi ci interessano intrinsecamente le proprietà fisiche, per tesserli, stamparli o modellarli.
I primi materiali plastici
L’onda di marea di queste nuove sostanze plastiche cominciò ad alzarsi impercettibilmente in un’occasione “ludica”. Negli Stati Uniti era stato offerto un premio di 10.000 $ per chi avesse trovato un materiale sostitutivo dell’avorio, di cui si avvertiva grande penuria per la fabbricazione delle palle da biliardo. John Wesley Hyatt (1837-1920) puntò a vincere il premio e, fra le varie sostanze prese in considerazione, studiò la nitrocellulosà; egli scoprì che la soluzione di canfora in etanolo era un solvente perfetto e un plastificante ideale della nitrocellulosà. Nel 1872 Hyatt mise in commercio i primi articoli di celluloide, una soluzione solida di nitrocellulosà e canfora; malgrado l’estrema infiammabilità, l’eccellente stabilità dimensionale della celluloide la rese insostituibile nei lavori fotografici di precisione, fin quando fu sostituita nel secondo dopoguerra dal triacetato di cellulosa, molto meno infiammabile.
Un secondo materiale plastico destinato a una lunghissima vita sul mercato fu ottenuto da Leo H. Baekeland (1863-1944), un geniale chimico belga trapiantato negli Stati Uniti, che con i suoi brevetti del 1907 aprì il nuovo settore delle sostanze termoplastiche. All’inizio del nostro secolo aveva già guadagnato – come dicono gli americani – il suo primo milione di dollari cedendo a G. Eastman il brevetto di una speciale carta fotografica, e si era concesso un periodo di studio a Berlino. Di ritorno negli Stati Uniti aveva costatato che il suo paese d’adozione importava 27 milioni di chilogrammi di gomma lacca, e si era impegnato nella ricerca di un sostituto. La reazione fra fenolo e formaldeide era già stata molto studiata, fin da quando Baeyer aveva segnalato nel 1871 la formazione di una sostanza scura e catramosa, ma nessuno era giunto a controllarla con la maestria di Baekeland: in presenza di alcali aveva ottenuto un materiale resinoso che una volta riscaldato diventava duro, insolubile e non più fusibile. Il nuovo materiale era un ottimo isolante; immesso in stampi sotto forma di polvere dava per un semplice aumento di temperatura oggetti di buona resistenza meccanica, sagomati e complessi a piacere. Come si è detto il successo della bachelite fu duraturo; al momento della morte del suo scopritore erano prodotte in tutto il mondo 125.000 t di resine fenoliche.
La seta artificiale
Le ambizioni iniziali di Hyatt e Baekeland erano relativamente modeste: avorio e gomma lacca non servivano certo a consumi di massa. Qui l’inizio della sostituzione avvenne in un territorio classico, quello dell’industria tessile, e germinò da un’intenzione affatto lontana: la produzione di filamenti adatti alle lampade a incandescenza di Edison. Il materiale di partenza dell’inglese J.W. Swan (1828-1914) fu ancora una volta la nitrocellulosà; egli ottenne i primi filamenti nel 1883 iniettando in acido acetico una soluzione di nitrocellulosà. Gli schizzi di soluzione coagulavano in filamenti che Swan successivamente carbonizzava, essiccava e montava su supporti isolanti. La stessa traccia fu seguita in Francia da Hilaire Bernigaud de Chardonnet (1839-1924), un discepolo di Pasteur; egli disciolse il dinitrato di cellulosa in alcool e etere; la soluzione, molto densa, veniva forzata attraverso una filiera in un apposito bagno, ed era così ottenuta una “seta artificiale” commerciabile. I nuovi tessuti spuntarono un certo successo perché la fibra era estremamente lucente, ma erano anche piuttosto pericolosi per l’infiammabilità intrinseca della nuova fibra.
Con l’innovazione di Chardonnet l’idea tecnica di base era formulata con chiarezza: dissolvere la cellulosa o qualche altra sostanza simile in una soluzione viscosa e trafilarla in fibre. Il passo successivo – e fondamentale – si realizzò in Inghilterra a opera di due chimici industriali, C.F. Cross (1855-1935) e E.J. Bevan (1856-1921). Essi erano nei primi anni 1880 i maggiori esperti mondiali dell’industria della cellulosa e della carta; nel loro laboratorio privato scoprirono che la cellulosa, trattata con soda, reagisce con il solfuro di carbonio dando un composto solubile in acqua (debolmente alcalina). La soluzione sciropposa {viscosa) poteva dare una fibra continua se iniettata in un bagno di acido solforico e solfato di sodio (1892). L’utilizzazione industriale del processo di Cross e Bevan incontrò non poche difficoltà, ma esso aveva “grandi potenzialità in quanto richiedeva come punto di partenza la stessa pasta di legno dell’industria della carta, e non la costosa cellulosa del cotone. Il brevetto fu ceduto a Samuel Courtaulds, che avviò la produzione nel 1906; alla vigilia della prima guerra mondiale questo processo controllava l’8o% del mercato della seta artificiale.
La storia della produzione di questa fibra è importante anche perché costituisce un caso particolare di pluralismo tecnologico. Sono infatti da ricordare altri due processi: quello che solubilizzava la cellulosa mediante anidride acetica, avviato in Germania nel 1902 e fiorito nel primo dopoguerra, e quello basato su una soluzione cuproammoniacale di cellulosa, il cui prodotto divenne noto sotto il nome di seta Bemberg (1911).
La convergenza dei diversi processi portò a un vero boom postbellico delle fibre derivate dalla cellulosa: nel 1919 la produzione mondiale era di 11.000 t, dieci anni dopo era salita a 197.000 t. Nel 1933 il pluralismo tecnologico si attenuò con la chiusura degli impianti Chardonnet, mentre alla fine degli anni ’30 il processo alla viscosa dominava più dei 4/5 della produzione. Ma allora si stavano già producendo i primi campioni di nylon, ed era iniziata una storia diversa, quella delle fibre totalmente sintetiche.
La nascita della chimica macromolecolare
La chimica macromolecolare fu fondata con un lavoro duro e appassionato da Hermann Staudinger (1881-1965), che fra il 1922 e il 1932 dovette sostenere una lotta estenuante all’interno della comunità scientifica tedesca per affermare il concetto stesso di macromolecola. Ancora nel 1926, in un grande congresso scientifico a Düsseldorf, apparve completamente isolato; tuttavia a questo isolamento accademico faceva riscontro una forte integrazione con gli interessi della grande industria chimica. Fra i maggiori frutti di questa collaborazione dobbiamo ricordare la produzione di massa del Buna-S 5.000 t nel 1938), un elastomero che si otteneva dalla co-polimerizzazione del butadiene e dello stirene, e che si dimostrò un buon sostituto del caucciù. L’interesse della Bayer alla ricerca sulla gomma sintetica risaliva al 1906, però il crollo dei prezzi del prodotto naturale dopo il 1910 aveva messo in ombra l’ipotesi di uno sviluppo commerciale. La situazione drammatica dei rifornimenti durante la guerra aveva permesso la produzione di 2.350 t di gomma metile, derivata dalla polimerizzazione di 2,3-dimetilbutadiene. Il progresso fra questa situazione e quella nella seconda guerra mondiale può essere visto (oltre che nella qualità del prodotto) nei tempi di polimerizzazione. Per la gomma metile erano necessari da 3 a 5 mesi per la polimerizzazione al 97% di una carica; nel primo dopoguerra l’impiego del butadiene e del sodio come catalizzatore fece scendere i tempi a due settimane. Il passo decisivo avvenne nel 1927 quando alla Bayer (allora “inclusa” nell’IG Farben) venne messa a punto la nuova tecnologia della polimerizzazione in emulsione; durante la seconda guerra mondiale la reazione richiedeva solo più 30 ore negli impianti tedeschi di Schkopau, e appena 14 negli Stati Uniti. Qui, oltre Atlantico, la situazione delle applicazioni della chimica macromolecolare era piuttosto diversa da quella tedesca.
Le ricerche sviluppate da W.H. Carothers (1896-1937) per conto della Du Pont a partire dal 1928, pur condotte in un laboratorio industriale furono più specializzate, e in un certo senso più eleganti di quelle di Staudinger. Ne derivarono due prodotti di qualità; nel 1931 Carothers sintetizzò un elastomero derivato dal cloroprene; esso fu commercializzato come gomma per usi speciali (neoprene) nel 1935, anno in cui il chimico della Du Pont brevettò una serie di nuovi polimeri poliamidici. La produzione del nylon 66 iniziò nel 1938, dopo quattro anni di lavoro di sviluppo, costato alla Du Pont 27 milioni di dollari. Malgrado questi successi (o forse proprio per questi!) al momento dell’invasione giapponese delle Indie olandesi gli Stati Uniti non possedevano conoscenze “indigene” atte a sopperire ai mancati rifornimenti di caucciù; la produzione a scopi militari di gomma sintetica fu quindi alimentata con i brevetti del Buna-S. Al termine della guerra la produzione mondiale di Buna-S era di 756.000 t all’anno, quella di neoprene di 45.000 t.
PVC, polietilene e polipropilene
Già le vicende del Buna-S e del nylon ci hanno messo sull’avviso che lunghi tempi di ricerca e sviluppo, e ingentissimi investimenti, erano divenuti componenti essenziali delle innovazioni legate ai nuovi materiali. Prima di fare qualche osservazione a questo proposito ci soffermeremo ancora su tre “casi”: PVC, polietilene e polipropilene.
La prima sintesi del cloruro di vinile risale alle ricerche giovanili di H. Regnault (1810-1878), condotte nel 1835 nel laboratorio di Liebig. Le proprietà di polimerizzazione di questa sostanza rimasero incontrollabili fin quando un chimico industriale della Höchst, Fritz Klatte, prese – fra il 1912 e il 1913 – una serie di brevetti che puntavano alla fotopolimerizzazione del cloruro di vinile; il polivinilcloruro così ottenuto risultava essere un materiale intrattabile: instabile alla luce, duro da lavorare, e poteva liberare acido cloridrico se riscaldato. Fu nei laboratori dell’IG Farben che si trovò una soluzione a tutti questi problemi, man man che divenivano accessibili i fondamenti della chimica macromolecolare di Staudinger. Il passo fondamentale fu compiuto nei laboratori di Ludwigshafen (1929-31), con il trasferimento alla sintesi del PVC delle conoscenze acquisite nella polimerizzazione in emulsione del Buna-S. La commercializzazione iniziata nel 1933 poteva avviarsi anche per l’intensa ricerca condotta dalla ig Farben sui plastificanti del PVC, che lo trasformavano in un materiale adatto agli usi più svariati. Del tutto diverso fu il contesto scientifìco-tecnico in cui venne alla luce il polietilene. L’Alcali Division della Imperial Chemical Industries aveva forti tradizioni di ricerca, ereditate dall’impresa di Mond che vi era stata incorporata al momento della formazione della ICI nel 1926. Proprio alla vigilia della fondazione dell’oligopolio inglese aveva iniziato a lavorarvi un giovane chimico, R.O. Gibson, già allievo di A. Michels, uno studioso olandese delle tecniche di sintesi ad altissime pressioni. Il progetto di ricerca fondamentale era nato da un interesse verso il processo Haber, ed era rivolto allo studio delle reazioni di addizione fra etilene e altre molecole quali la benzaldeide. I primi reattori disegnati da Michels furono installati nei laboratori di Winnington nel 1931, e il 27 marzo 1933 fu notato che una cera bianca ricopriva le pareti di un recipiente che aveva contenuto etilene e benzaldeide a una pressione (incerta!) fra le 1.000 e le 2.000 atmosfere; l’analisi rivelò che era un polimero dell’etilene, ma solo nel dicembre del 1935 l’etilene fu fatto reagire da solo, con l’ottenimento di 8 g di polimero. A questo punto il problema tecnico di rendere il processo sicuro, con compressori affidabili, occupò la lei fino al marzo 1938, quando fu avviata la preparazione su piccola scala. La prima tonnellata di materiale dimostrò che questo aveva qualità impareggiabili come isolante elettrico, e nell’agosto del 1939 iniziò la produzione industriale, che fu interamente assorbita dalle necessità belliche (in particolare nelle tecniche collegate al radar). Finita la guerra il polietilene rischiò di scomparire dai prodotti della ICI, ma i risultati delle ricerche su possibili nuove applicazioni dimostrarono che il polietilene era un materiale assai più versatile di quanto si fosse pensato. E d’altra parte uno sviluppo imprevisto venne dalle ricerche di Karl Ziegler (1898-1973).
Ziegler si era occupato nel 1928 dell’attività catalitica del sodio nella preparazione del Buna, e non aveva mai abbandonato il campo dei composti metallorganici. Dal 1945 si era dedicato a ricerche sui composti organici dell’alluminio, e nel 1953 stava cercando di sintetizzare derivati tri-alchilici superiori dell’alluminio scaldando i termini inferiori con etilene, quando si imbattè in un risultato sorprendente: la dimerizzazione completa dell’etilene in butilene. Seguendo questa traccia Ziegler scoprì che il tetracloruro di titanio favoriva la formazione di alti polimeri lineari dell’etilene in condizioni di temperatura e pressione assai blande. Era l’inizio di una vera rivoluzione, non solo per il nuovo processo di sintesi del polietilene (Höchst, 1955), ma anche per il formidabile effetto amplificatore di queste scoperte nel laboratorio milanese di Giulio Natta (1903-1979), che da tempo era in contatto con Ziegler attraverso la mediazione della Montecatini. Natta estese la reazione di Ziegler al propilene, scoprendo un’intera nuova classe di polimeri, e spiegandone le eccezionali proprietà attraverso una precisa indagine strutturale. La Montecatini cominciò la produzione commerciale del polipropilene nel 1957. Nel 1962 la produzione mondiale del polietilene ad alta densità di Ziegler e del polipropilene di Natta raggiungeva le 250.000 t; l’anno successivo i due scienziati ricevettero congiuntamente il premio Nobel per la chimica.
Siamo ora in grado di fare un paio di osservazioni. I processi di innovazione con cui i nuovi materiali polimerici furono portati sul mercato sono stati tortuosi, punteggiati da eventi inaspettati, e spesso vissuti dalle imprese con ritmi decennali. Sono i segni vistosi di una rivoluzione scientifica, che metteva in discussione il concetto classico di molecola e di una rivoluzione tecnica coeva, che doveva gestire nello stesso momento nuovi processi e nuovi prodotti. Un’analisi attenta e puntuale dei principali “avanzamenti tecnici” nel periodo fino al 1955 (117 in tutto) ha dimostrato la presenza dominante di tre soli paesi, e quella rilevante di poche grandi imprese: su un totale di 51 innovazioni originate in Germania, 30 si erano realizzate all’interno dell’IG Farben; sul totale americano di 43 la Du Pont ne poteva rivendicare 12; in Inghilterra 7 innovazioni su 15 avevano avuto origine all’interno della lei. A tutti gli altri paesi rimanevano solo 8 innovazioni.
Per quanto riguarda i tempi di trasferimento delle scoperte di laboratorio alla produzione industriale, la commercializzazione dei risultati di Ziegler e Natta appare particolarmente rapida. A questo hanno contribuito diversi fattori: innanzi tutto le condizioni blande in cui si realizzavano le reazioni di polimerizzazione, e un generale progresso delle pratiche costruttive degli impianti chimici, ma forse il fattore essenziale è stato la flessibilità conseguita dall’industria petrolchimica nella produzione delle diverse classi di idrocarburi.
CHIMICA ORGANICA E INDUSTRIA: ONDA DI MAREA (1870-1970)
DAL PETROLIO AL CARBONe
Lo sviluppo dell’industria petrolifera e i processi di cracking
Le vicende dell’industria petrolifera e di quella chimica rimasero a lungo separate. Fino ai primi anni del nostro secolo le raffinerie di petrolio avevano il compito esclusivo di distillare il greggio per separare le varie frazioni di idrocarburi e commercializzarle per i diversi usi. Questi usi non avevano affatto domande bilanciate: fra il 1890 e il 1900 vi fu penuria della frazione a 10-15 atomi di carbonio (cherosene) ed eccesso di quella a 6-10 atomi di carbonio (benzina). Il cherosene era richiestissimo per le lampade a petrolio, mentre la benzina era ritenuta troppo pericolosa per la sua infiammabilità ed era in genere scaricata nei fiumi. Con l'”avvento” dell’automobile e la diffusione dell’illuminazione elettrica la situazione mutò radicalmente, e ritornò d’attualità una proposta fatta molti anni prima: spezzare termicamente le catene degli idrocarburi più pesanti per ottenere frazioni più leggere, a catena più corta. Il primo processo di cracking termico che diede risultati commerciali (e quali risultati!) fu realizzato negli Stati Uniti da W.M. Burton (1865-1954), direttore di una raffineria della Standard. Gli impianti pilota, che operavano a 4-5 atmosfere, presentarono grandi difficoltà costruttive ed erano piuttosto pericolosi, così che nel 1910 la direzione della Standard rifiutò di autorizzare la spesa per un impianto commerciale. Tuttavia nel 1911 la legge antitrust americana scisse la Standard Oil in diversi tronconi, e la nuova direzione aziendale favorì l’investimento. Il processo fu avviato nel 1913, ed è stato calcolato che i costi di sviluppo (236.000 $) furono ripagati io volte nel primo anno operativo dell’impianto. Il metodo Burton dominò il settore fino al 1920-1921, periodo in cui furono proposti ben nove processi, fra cui risultò importantissimo quello di C.P. Dubbs (1881-1962). Dubbs era figlio d’arte (le iniziali del nome corrispondono a Carbon Petroleum), e da un facoltoso finanziatore fece acquistare alcuni brevetti di suo padre, che allora dirigeva una piccola raffineria californiana. I brevetti erano stati presi per il trattamento del greggio californiano, ma Dubbs junior vi aveva visto la possibilità di migliorare il processo Burton, in particolare rendendolo continuo. I cinque anni che furono necessari per la messa a punto del processo richiesero 6 milioni di dollari di spese di sviluppo (mandando in rovina il finanziatore di Dubbs), tuttavia il nuovo metodo, funzionante a partire dal 1923, era effettivamente molto più efficiente di quello di Burton.
Negli anni ’20 diverse compagnie petrolifere incominciarono a interessarsi delle potenzialità che la catalisi offriva al processo di cracking, ma lo fecero senza entusiasmo e con magrissimi risultati. Nel 1925 un ingegnere francese, Eugène Houdry, intraprese una ricerca sistematica dell’effetto sul cracking di centinaia di catalizzatori, e nel 1927 ottenne i primi risultati positivi. Houdry aveva investito nella ricerca una parte ingente della sua fortuna personale, ma presto la scala delle ricerche di sviluppo divenne tale da richiedere l’esperienza impiantistica e i capitali di una grande impresa. Privo di appoggi in Francia emigrò negli Stati Uniti, dove costituì una società con la Socony Vacuum Oil (1930), cui si aggiunse più tardi la Sun Oil (1932). Il processo cominciò a funzionare a livello industriale fra il 1936 e il 1937, dopo che erano stati investiti circa 11 milioni di dollari (3 provenienti dal patrimonio privato di Houdry).
Fin dagli inizi fu chiaro che lo stesso processo Houdry poteva essere perfezionato, in quanto era semi-continuo e con catalizzatore a letto fisso, e la “minaccia” di questa innovazione era tale che nel 1938 fu formato un gruppo, denominato Catalytic Research Associates, che coordinava gli sforzi di ricerca di giganti quali l’Indiana Standard, la Jersey Standard, la Shell e la Texaco. Il processo a letto fluido divenne operativo nel 1942; al termine di una serie di perfezionamenti nel 1952 era costato 30 milioni di dollari di investimenti in ricerca e sviluppo.
La transizione dal carbone al petrolio
Come si è visto si trattò di una (costosa) vicenda interna all’industria petrolifera, e tale rimase il suo risultato tecnicamente più valido, il cracking catalitico, ancora migliorato dal punto di vista della produzione di combustibili con l’introduzione dei catalizzatori zeolitici (1965). Il cracking termico invece ha permesso una svolta radicale nei rifornimenti di materie prime all’industria chimica, e ha dato un impeto violento alla produzione di materie plastiche.
L’accessibilità alle materie prime è stata sempre la prima comprensibilissima preoccupazione in tutti i settori produttivi, ma in quello chimico questa preoccupazione è esasperata dal fatto che un singolo nuovo processo può esaurire – di colpo – tutte le risorse disponibili in un certo settore di “intermedi”. Così la ig Farben affidò a un chimico di genio, Walter Reppe, il compito di sintetizzare a partire dall’acetilene il butadiene necessario per il Buna. Fra il 1926 e il 1930 Reppe risolse il problema con un metodo basato su quattro reazioni successive, di cui una era un’idrogenazione da alta pressione (una reazione ubiqua), e tre richiedevano catalizzatori specifici. L’acetilene era ricavato a sua volta dal carburo di calcio, e l’intero sistema tecnico del Buna-S si basava su intermedi provenienti in modo più o meno mediato dal carbone.
Dopo la fine della seconda guerra mondiale la formazione di un nuovo mercato mondiale svaporò gli spettri dell’autarchia nelle grandi economie capitalistiche, e gli sviluppi dell’industria petrolifera che abbiamo appena descritti dettarono una nuova interpretazione del problema degli intermedi, così che, per gradi, si passò dal “tutto dal carbone” al “tutto dal petrolio”. Il passaggio fu favorito anche da un altro fatto: gli intermedi richiesti per le nuove sostanze plastiche erano ottenuti con forti economie di scala impiegando i procedimenti petrolchimici. Un caso emblematico chiarirà la svolta degli anni 1950.
Quando la ICI iniziò a produrre il polietilene l’impianto era progettato per una produzione annua di 50 t, e l’etilene era ricavato da alcool etilico di fermentazione. Nel 1952 la produzione di 2.000 t annue di polietilene era impiegata ancora per usi speciali; l’etilene ricavato da fermentazione portava i costi a 250 sterline per tonnellata: il passaggio all’etilene da cracking significò una caduta dei costi a 90 sterline per tonnellata. Ulteriori vantaggi si ebbero spingendo verso l’alto la scala degli impianti; secondo calcoli del 1963 il costo per tonnellata di etilene da cracking sarebbe stato di 22 sterline per tonnellata con un impianto da 50.000 t/anno, e sarebbe sceso a 16 sterline con una produzione annua di 300.000 t. Su questa base tecnico-economica, imperniata sull’ottenimento di “alifatici” mediante cracking, e sulla produzione di massa di materie plastiche si sarebbe stabilizzato in buona parte quel paesaggio industriale della chimica che è giunto ai giorni nostri.
|
|
I NYLON
Ricerca elaborata presso il Liceo Bramante di Magenta
1 Comment
[…] Materie plastiche […]